耐熱塗装工程
第一耐熱塗装ライン
第一耐熱塗装ラインの特徴
180mのトローリーコンベアのラインで、脱脂、洗浄、化成被膜形成、耐熱塗装、焼成を一貫して行っており、製品の掛けから脱までが90分にて作業が完了するラインです。常時2マン体制で耐熱塗装を行っていますので、様々な要望にお応えできる耐熱塗装ラインとなっています。
製造工程
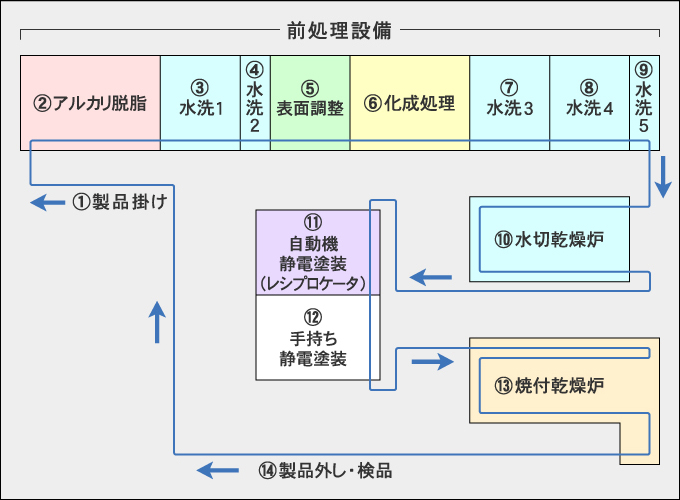
まずは、製品を耐熱塗装ラインに掛けるところから始まります。製品を受注する段階で、汎用塗装治具を使用するか、専用塗装治具を作成するか判断し、一貫して同じ治具を使用して耐熱塗装していきます。
ミリオン化学(株)製のアルカリ脱脂液(グランダークリーナー)を使用し、シャワーにて油分、ゴミを除去します。片側13本のライザー管で、1本につき5個のシャワーノズル、全体で130個のシャワーノズルにて洗浄しています。 アルカリ性洗浄剤についてはこちら
アルカリ脱脂液を洗い流すための水洗を行います。片側4本のライザー管で、1本につき5個のシャワーノズル、全体で40個のシャワーノズルにて洗浄しています。
水道直結のライザー管2本で洗浄を行っています。
ミリオン化学(株)製の表面調整液(グランダーファイナー)を使用し、素材の表面調整を行います。片側4本のライザー管で、1本につき5個のシャワーノズル、全体で40個のシャワーノズルにて表面調整しています。
均一できめの細かい化成被膜を形成するためには欠かせない工程です。
ミリオン化学(株)製の化成被膜液(グランダー)を使用し、被膜形成用シャワーにてリン酸亜鉛皮膜を形成させます。片側13本のライザー管で、1本につき5個の被膜形成用ノズル、全体で130個のノズルにて被膜形成しています。
化成被膜液を洗い流すための水洗を行います。片側4本のライザー管で、1本につき5個のシャワーノズル、全体で40個のシャワーノズルにて洗浄しています。
洗浄工程内最後の水洗です。片側4本のライザー管で、1本につき5個のシャワーノズル、全体で40個のシャワーノズルにて洗浄しています。ここで、素材表面は十分に洗浄できていますが、次の水洗工程へつながります。
水道直結のライザー管2本で洗浄を行っています。最終の最終で、完全に洗浄を行う予備の水洗です。
素材表面に水分が残っていると必要な塗膜形成ができません。この工程で、製品を完全に乾かします。110℃15分で設定しています。
センサーで製品の形状を認識し、その幅に合わせて静電自動塗装機にて塗装する工程です。
4丁のスプレーノズルから塗料を塗布し、静電塗装の方式で塗装を行っているので、
また、この工程で全面塗装の必要ない製品に関しては、塗りにくい部分だけ、カップガンにて補正塗装を行っています。
ハンド静電ガンにて仕上げ塗装を行っています。噴出させた塗料がどれだけ製品に付着するのかということを、塗着効率といいます。塗装器具でスタンダードなカップガンにて塗装する場合、塗着効率は15%といわれています。つまり、85%は製品に付着せずに捨てている状況です。
静電塗装で行うと、製品の形状にもよりますが、60%の塗着効率があるといわれています。この塗着効率の高い、静電塗装という方式で、当社技術者が塗装を行っています。
塗装ブース裏手に焼付乾燥炉があり、そこで塗料の仕様書の設定温度で20分焼付を行っています。
焼付が終わった製品を専用治具から外し、検品後パレットに入れていく工程です。ここで、耐熱塗装の不具合などを選別していきます。社内で後工程がある場合は、社内移動用荷姿。出荷になる場合は、出荷荷姿にて出荷していきます。すべて決められた荷姿になっています。
基本的には梱包荷姿はお客様の生産管理との打ち合わせ事項となっていますが、「キズつかないように入れて」という指示が多く、
第二耐熱塗装ライン
特徴
90mのトローリーコンベアのラインで、自動塗装機のみで耐熱塗装を行って、焼成するラインとなっています。基本的に、第二耐熱塗装ラインでは耐熱ものを製造しており、狭く細長い焼成炉を使用しているため、省エネ設計の耐熱塗装ラインとなっています。
第一耐熱塗装ラインに比べ、比較的重い製品を掛けるように設計されており、日産のGT-Rもこのラインで塗装されています。
製造工程
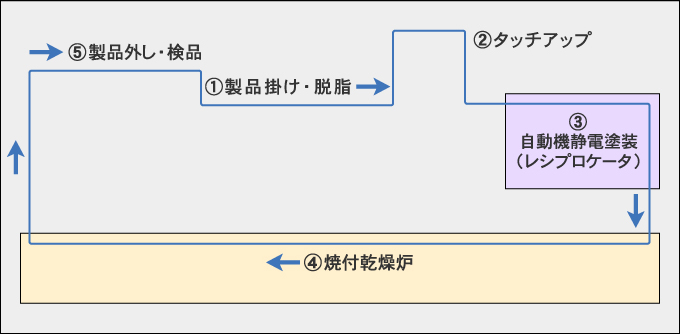
専用塗装治具もしくは汎用塗装治具にて、製品をトローリーコンベアに引っ掛けます。第二耐熱塗装ラインには自動の洗浄設備がないので、溶剤を含ませたウエスで拭き取り洗浄を行っています。
このラインに掛かるものは、溶接工程を経たものが多くあります。その溶接部は鉄素材が酸化しており、より強力な塗膜を必要とするので、自動塗装機で塗装をする前に、溶接部のタッチアップを行っています。塗装が自動機のみなので、欠かせない工程です。塗料は本塗りの塗料を共色です。
センサーにて製品の幅、高さ、形状を認識して、塗装を行う、全くの自動塗装ラインです。この前工程で、タッチアップでの補助塗装は行いますが、ラインで流れる製品がマフラを中心に行っているのでこの耐熱塗装方法が可能になっています。
マフラというものは円筒上の製品が多く(つまりジュースの缶を大きくしたものといえば想像つきやすいかもしれません)。その円筒状の製品は静電効率が非常に高く、正面からの塗装でどんどん塗装面の反対側まで耐熱塗装が回り込んでいきます。
静電塗装の効果が大きく発揮された耐熱塗装設備になっています。
ラインが上下に分かれていて、下が製品を掛けて、外す場所で、その上を乾燥炉が乗っかっているというイメージです。塗料の指定温度で20分焼成する工程です。
焼付が終わった製品を専用治具から外し、検品後パレットに入れていく工程です。ここで、耐熱塗装の不具合などを選別していきます。